Tuesday, December 15, 2009
There are two common classes of control systems, with many variations and combinations: logic or sequential controls, and feedback or linear controls. There is also fuzzy logic, which attempts to combine some of the design simplicity of logic with the utility of linear control. Some devices or systems are inherently not controllable.
Overview
The term "control system" may be applied to the essentially manual controls that allow an operator to, for example, close and open a hydraulic press, where the logic requires that it cannot be moved unless safety guards are in place.
An automatic sequential control system may trigger a series of mechanical actuators in the correct sequence to perform a task. For example various electric and pneumatic transducers may fold and glue a cardboard box, fill it with product and then seal it in an automatic packaging machine.
In the case of linear feedback systems, a control loop, including sensors, control algorithms and actuators, is arranged in such a fashion as to try to regulate a variable at a setpoint or reference value. An example of this may increase the fuel supply to a furnace when a measured temperature drops. PID controllers are common and effective in cases such as this. Control systems that include some sensing of the results they are trying to achieve are making use of feedback and so can, to some extent, adapt to varying circumstances. Open-loop control systems do not directly make use of feedback, but run only in pre-arranged ways.
Logic control
Pure logic control systems were historically implemented by electricians with networks of relays, and designed with a notation called ladder logic. Today, most such systems are constructed with programmable logic devices or microcontrollers.
Logic controllers may respond to switches, light sensors, pressure switches etc and cause the machinery to perform some operation. Logic systems are used to sequence mechanical operations in many applications. Examples include elevators, washing machines and other systems with interrelated stop-go operations.
Logic systems are quite easy to design, and can handle very complex operations. Some aspects of logic system design make use of Boolean logic.
On–off control
For example, a thermostat is a simple negative-feedback control: when the temperature (the "measured variable" or MV) goes below a set point (SP), the heater is switched on. Another example could be a pressure switch on an air compressor: when the pressure (MV) drops below the threshold (SP), the pump is powered. Refrigerators and vacuum pumps contain similar mechanisms operating in reverse, but still providing negative feedback to correct errors.
Simple on–off feedback control systems like these are cheap and effective. In some cases, like the simple compressor example, they may represent a good design choice.
In most applications of on–off feedback control, some consideration needs to be given to other costs, such as wear and tear of control valves and maybe other start-up costs when power is reapplied each time the MV drops. Therefore, practical on–off control systems are designed to include hysteresis, usually in the form of a deadband, a region around the setpoint value in which no control action occurs. The width of deadband may be adjustable or programmable.
Linear control
Linear control systems use linear negative feedback to produce a control signal mathematically based on other variables, with a view to maintaining the controlled process within an acceptable operating range.
The output from a linear control system into the controlled process may be in the form of a directly variable signal, such as a valve that may be 0 or 100% open or anywhere in between. Sometimes this is not feasible and so, after calculating the current required corrective signal, a linear control system may repeatedly switch an actuator, such as a pump, motor or heater, fully on and then fully off again, regulating the duty cycle using pulse-width modulation.
Proportional control
When controlling the temperature of an industrial furnace, it is usually better to control the opening of the fuel valve in proportion to the current needs of the furnace. This helps avoid thermal shocks and applies heat more effectively.
Proportional negative-feedback systems are based on the difference between the required set point (SP) and measured value (MV) of the controlled variable. This difference is called the error. Power is applied in direct proportion to the current measured error, in the correct sense so as to tend to reduce the error (and so avoid positive feedback). The amount of corrective action that is applied for a given error is set by the gain or sensitivity of the control system.
At low gains, only a small corrective action is applied when errors are detected: the system may be safe and stable, but may be sluggish in response to changing conditions; errors will remain uncorrected for relatively long periods of time: it is over-damped. If the proportional gain is increased, such systems become more responsive and errors are dealt with more quickly. There is an optimal value for the gain setting when the overall system is said to be critically damped. Increases in loop gain beyond this point will lead to oscillations in the MV; such a system is under-damped.
Under-damped furnace example
In the furnace example, suppose the temperature is increasing towards a set point at which, say, 50% of the available power will be required for steady-state. At low temperatures, 100% of available power is applied. When the MV is within, say 10° of the SP the heat input begins to be reduced by the proportional controller. (Note that this implies a 20° "proportional band" (PB) from full to no power input, evenly spread around the setpoint value). At the setpoint the controller will be applying 50% power as required, but stray stored heat within the heater sub-system and in the walls of the furnace will keep the measured temperature rising beyond what is required. At 10° above SP, we reach the top of the proportional band (PB) and no power is applied, but the temperature may continue to rise even further before beginning to fall back. Eventually as the MV falls back into the PB, heat is applied again, but now the heater and the furnace walls are too cool and the temperature falls too low before its fall is arrested, so that the oscillations continue.
Over-damped furnace example
The temperature oscillations that an under-damped furnace control system produces are unacceptable for many reasons, including the waste of fuel and time (each oscillation cycle may take many minutes), as well as the likelihood of seriously overheating both the furnace and its contents.
Suppose that the gain of the control system is reduced drastically and it is restarted. As the temperature approaches, say 30° below SP (60° proportional band or PB now), the heat input begins to be reduced, the rate of heating of the furnace has time to slow and, as the heat is still further reduced, it eventually is brought up to set point, just as 50% power input is reached and the furnace is operating as required. There was some wasted time while the furnace crept to its final temperature using only 52% then 51% of available power, but at least no harm was done. By carefully increasing the gain (i.e. reducing the width of the PB) this over-damped and sluggish behavior can be improved until the system is critically damped for this SP temperature. Doing this is known as 'tuning' the control system. A well-tuned proportional furnace temperature control system will usually be more effective than on-off control, but will still respond slower than the furnace could under skillful manual control.
PID control
Main article: PID controller
Apart from sluggish performance to avoid oscillations, another problem with proportional-only control is that power application is always in direct proportion to the error. In the example above we assumed that the set temperature could be maintained with 50% power. What happens if the furnace is required in a different application where a higher set temperature will require 80% power to maintain it? If the gain was finally set to a 50° PB, then 80% power will not be applied unless the furnace is 15° below setpoint, so for this other application the operators will have to remember always to set the setpoint temperature 15° higher than actually needed. This 15° figure is not completely constant either: it will depend on the surrounding ambient temperature, as well as other factors that affect heat loss from or absorption within the furnace.
To resolve these two problems, many feedback control schemes include mathematical extensions to improve performance. The most common extensions lead to proportional-integral-derivative control, or PID control (pronounced pee-eye-dee).
Derivative action
The derivative part is concerned with the rate-of-change of the error with time: If the measured variable approaches the setpoint rapidly, then the actuator is backed off early to allow it to coast to the required level; conversely if the measured value begins to move rapidly away from the setpoint, extra effort is applied—in proportion to that rapidity—to try to maintain it.
Derivative action makes a control system behave much more intelligently. On systems like the temperature of a furnace, or perhaps the motion-control of a heavy item like a gun or camera on a moving vehicle, the derivative action of a well-tuned PID controller can allow it to reach and maintain a setpoint better than most skilled human operators could.
If derivative action is over-applied, it can lead to oscillations too. An example would be a MV that increased rapidly towards SP, then halted early and seemed to "shy away" from the setpoint before rising towards it again.
Integral action
The integral term magnifies the effect of long-term steady-state errors, applying ever-increasing effort until they reduce to zero. In the example of the furnace above working at various temperatures, if the heat being applied does not bring the furnace up to setpoint, for whatever reason, integral action increasingly moves the proportional band relative to the setpoint until the time-integral of the MV error is reduced to zero and the setpoint is achieved.
Other techniques
Another common technique is to filter the MV or error signal. Such a filter can reduce the response of the system to undesirable frequencies, to help eliminate instability or oscillations. Some feedback systems will oscillate at just one frequency. By filtering out that frequency, one can use very "stiff" feedback and the system can be very responsive without shaking itself apart.
The most complex linear control systems developed to date are in oil refineries[citation needed] (model predictive control). The chemical reaction paths and control systems are normally designed together using specialized computer-aided-design software.
Feedback systems can be combined in many ways. One example is cascade control in which one control loop applies control algorithms to a measured variable against a setpoint, but then actually outputs a setpoint to another controller, rather than affecting power input directly.
Usually if a system has several measurements to be controlled, feedback systems will be present for each of them.
Fuzzy logic
Fuzzy logic is an attempt to get the easy design of logic controllers and yet control continuously-varying systems. Basically, a measurement in a fuzzy logic system can be partly true, that is if yes is 1 and no is 0, a fuzzy measurement can be between 0 and 1.
The rules of the system are written in natural language and translated into fuzzy logic. For example, the design for a furnace would start with: "If the temperature is too high, reduce the fuel to the furnace. If the temperature is too low, increase the fuel to the furnace."
Measurements from the real world (such as the temperature of a furnace) are converted to values between 0 and 1 by seeing where they fall on a triangle. Usually the tip of the triangle is the maximum possible value which translates to "1."
Fuzzy logic then modifies Boolean logic to be arithmetical. Usually the "not" operation is "output = 1 - input," the "and" operation is "output = input.1 multiplied by input.2," and "or" is "output = 1 - ((1 - input.1) multiplied by (1 - input.2))."
The last step is to "defuzzify" an output. Basically, the fuzzy calculations make a value between zero and one. That number is used to select a value on a line whose slope and height converts the fuzzy value to a real-world output number. The number then controls real machinery.
If the triangles are defined correctly and rules are right the result can be a good control system.
When a robust fuzzy design is reduced into a single, quick calculation, it begins to resemble a conventional feedback loop solution. For this reason, many control engineers think one should not bother with it[citation needed]. However, the fuzzy logic paradigm may provide scalability for large control systems where conventional methods become unwieldy or costly to derive.
Fuzzy electronics is an electronic technology that uses fuzzy logic instead of the two-value logic more commonly used in digital electronics.
Physical implementations
Since modern small microcontrollers are so cheap (often less than $1 US), it's very common to implement control systems, including feedback loops, with computers, often in an embedded system. The feedback controls are simulated by having the computer make periodic measurements and then calculating from this stream of measurements (see digital signal processing, sampled data systems).
Computers emulate logic devices by making measurements of switch inputs, calculating a logic function from these measurements and then sending the results out to electronically-controlled switches.
Logic systems and feedback controllers are usually implemented with programmable logic controllers which are devices available from electrical supply houses. They include a little computer and a simplified system for programming. Most often they are programmed with personal computers.
Logic controllers have also been constructed from relays, hydraulic and pneumatic devices, and electronics using both transistors and vacuum tubes vacuum tubes
Control Sysytem
For example, heating up the temperature in a room is a process that has the specific, desired outcome to reach and maintain a defined temperature (e.g. 20°C), kept constant over time. Here, the temperature is the controlled variable. At the same time, it is the input variable since it is measured by a thermometer and used to decide whether to heat or not to heat. The desired temperature (20°C) is the setpoint. The state of the heater (e.g. the setting of the valve allowing hot water to flow through it) is called the manipulated variable since it is subject to control actions.
A commonly used control device called a programmable logic controller, or a PLC, is used to read a set of digital and analog inputs, apply a set of logic statements, and generate a set of analog and digital outputs. Using the example in the previous paragraph, the room temperature would be an input to the PLC. The logical statements would compare the setpoint to the input temperature and determine whether more or less heating was necessary to keep the temperature constant. A PLC output would then either open or close the hot water valve, an incremental amount, depending on whether more or less hot water was needed. Larger more complex systems can be controlled by a Distributed Control System (DCS) or SCADA system.
In practice, process control systems can be characterized as one or more of the following forms:
Discrete – Found in many manufacturing, motion and packaging applications. Robotic assembly, such as that found in automotive production, can be characterized as discrete process control. Most discrete manufacturing involves the production of discrete pieces of product, such as metal stamping.
Batch – Some applications require that specific quantities of raw materials be combined in specific ways for particular durations to produce an intermediate or end result. One example is the production of adhesives and glues, which normally require the mixing of raw materials in a heated vessel for a period of time to form a quantity of end product. Other important examples are the production of food, beverages and medicine. Batch processes are generally used to produce a relatively low to intermediate quantity of product per year (a few pounds to millions of pounds).
Continuous – Often, a physical system is represented though variables that are smooth and uninterrupted in time. The control of the water temperature in a heating jacket, for example, is an example of continuous process control. Some important continuous processes are the production of fuels, chemicals and plastics. Continuous processes, in manufacturing, are used to produce very large quantities of product per year(millions to billions of pounds).
Applications having elements of discrete, batch and continuous process control are often called hybrid applications.
Statistical Process Control
Statistical Process Control (SPC) is an effective method of monitoring a process through the use of control charts. Much of its power lies in the ability to monitor both process center and its variation about that center. By collecting data from samples at various points within the process, variations in the process that may affect the quality of the end product or service can be detected and corrected, thus reducing waste as well as the likelihood that problems will be passed on to the customer. It has an emphasis on early detection and prevention of problems.
Examples
A thermostat is a simple example for a closed control loop: It constantly measures the current temperature and controls the heater's valve setting to increase or decrease the room temperature according to the user-defined setting. A simple method switches the heater either completely on, or completely off, and an overshoot and undershoot of the controlled temperature must be expected. A more expensive method varies the amount of heat provided by the heater depending on the difference between the required temperature (the "setpoint") and the actual temperature. This minimizes over/undershoot.
An anti-lock braking system (ABS) is a more complex example, consisting of multiple inputs, conditions and outputs.
Saturday, November 14, 2009
Refinig Process
Petroleum is a complex mixture of organic liquids called crude oil and natural gas, which occurs naturally in the ground and was formed millions of years ago. Crude oil varies from oilfield to oilfield in colour and composition, from a pale yellow low viscosity liquid to heavy black 'treacle' consistencies.
Crude oil and natural gas are extracted from the ground, on land or under the oceans, by sinking an oil well and are then transported by pipeline and/or ship to refineries where their components are processed into refined products. Crude oil and natural gas are of little use in their raw state; their value lies in what is created from them: fuels, lubricating oils, waxes, asphalt, petrochemicals and pipeline quality natural gas.
An oil refinery is an organised and coordinated arrangement of manufacturing processes designed to produce physical and chemical changes in crude oil to convert it into everyday products like petrol, diesel, lubricating oil, fuel oil and bitumen.
As crude oil comes from the well it contains a mixture of hydrocarbon compounds and relatively small quantities of other materials such as oxygen, nitrogen, sulphur, salt and water. In the refinery, most of these non - hydrocarbon substances are removed and the oil is broken down into its various components, and blended into useful products.
Natural gas from the well, while principally methane, contains quantities of other hydrocarbons - ethane, propane, butane, pentane and also carbon dioxide and water. These components are separated from the methane at a gas fractionation plant.
Petroleum hydrocarbon structures
Petroleum consists of three main hydrocarbon groups:
Paraffins
These consist of straight or branched carbon rings saturated with hydrogen atoms, the simplest of which is methane (CH4) the main ingredient of natural gas. Others in this group include ethane (C2H6), and propane (C3H8).
Hydrocarbons
With very few carbon atoms (C1 to C4) are light in density and are gases under normal atmospheric pressure. Chemically paraffins are very stable compounds.
Naphthenes
Naphthenes consist of carbon rings, sometimes with side chains, saturated with hydrogen atoms. Naphthenes are chemically stable, they occur naturally in crude oil and have properties similar to paraffins.
Aromatics
aromatic hydrocarbons are compounds that contain a ring of six carbon atoms with alternating double and single bonds and six attached hydrogen atoms. This type of structure is known as a benzene ring. They occur naturally in crude oil, and can also be created by the refining process.
The more carbon atoms a hydrocarbon molecule has, the "heavier" it is (the higher is its molecular weight) and the higher is its the boiling point.
Small quantities of a crude oil may be composed of compounds containing oxygen, nitrogen, sulphur and metals. Sulphur content ranges from traces to more than 5 per cent. If a crude oil contains appreciable quantities of sulphur it is called a sour crude; if it contains little or no sulphur it is called a sweet crude.
The refining process
Every refinery begins with the separation of crude oil into different fractions by distillation.
The fractions are further treated to convert them into mixtures of more useful saleable products by various methods such as cracking, reforming, alkylation, polymerisation and isomerisation. These mixtures of new compounds are then separated using methods such as fractionation and solvent extraction. Impurities are removed by various methods, e.g. dehydration, desalting, sulphur removal and hydrotreating.
Refinery processes have developed in response to changing market demands for certain products. With the advent of the internal combustion engine the main task of refineries became the production of petrol. The quantities of petrol available from distillation alone was insufficient to satisfy consumer demand. Refineries began to look for ways to produce more and better quality petrol. Two types of processes have been developed:
breaking down large, heavy hydrocarbon molecules
reshaping or rebuilding hydrocarbon molecules.
Distillation (Fractionation)
Because crude oil is a mixture of hydrocarbons with different boiling temperatures, it can be separated by distillation into groups of hydrocarbons that boil between two specified boiling points. Two types of distillation are performed: atmospheric and vacuum.
Atmospheric distillation takes place in a distilling column at or near atmospheric pressure. The crude oil is heated to 350 - 400oC and the vapour and liquid are piped into the distilling column. The liquid falls to the bottom and the vapour rises, passing through a series of perforated trays (sieve trays). Heavier hydrocarbons condense more quickly and settle on lower trays and lighter hydrocarbons remain as a vapour longer and condense on higher trays.
Liquid fractions are drawn from the trays and removed. In this way the light gases, methane, ethane, propane and butane pass out the top of the column, petrol is formed in the top trays, kerosene and gas oils in the middle, and fuel oils at the bottom. Residue drawn of the bottom may be burned as fuel, processed into lubricating oils, waxes and bitumen or used as feedstock for cracking units.
To recover additional heavy distillates from this residue, it may be piped to a second distillation column where the process is repeated under vacuum, called vacuum distillation. This allows heavy hydrocarbons with boiling points of 450oC and higher to be separated without them partly cracking into unwanted products such as coke and gas.
The heavy distillates recovered by vacuum distillation can be converted into lubricating oils by a variety of processes. The most common of these is called solvent extraction. In one version of this process the heavy distillate is washed with a liquid which does not dissolve in it but which dissolves (and so extracts) the non-lubricating oil components out of it. Another version uses a liquid which does not dissolve in it but which causes the non-lubricating oil components to precipitate (as an extract) from it. Other processes exist which remove impurities by adsorption onto a highly porous solid or which remove any waxes that may be present by causing them to crystallise and precipitate out.
Reforming
Reforming is a process which uses heat, pressure and a catalyst (usually containing platinum) to bring about chemical reactions which upgrade naphthas into high octane petrol and petrochemical feedstock. The naphthas are hydrocarbon mixtures containing many paraffins and naphthenes. In Australia, this naphtha feedstock comes from the crudes oil distillation or catalytic cracking processes, but overseas it also comes from thermal cracking and hydrocracking processes. Reforming converts a portion of these compounds to isoparaffins and aromatics, which are used to blend higher octane petrol.
paraffins are converted to isoparaffins
paraffins are converted to naphthenes
naphthenes are converted to aromatics
e.g.
heptane -> toluene + hydrogen
C7H16 -> C7H8 + 4H2
catalyst
cyclohexane -> benzene + hydrogen
C6H12 -> C6H6+ 3H2
Cracking
Cracking processes break down heavier hydrocarbon molecules (high boiling point oils) into lighter products such as petrol and diesel. These processes include catalytic cracking, thermal cracking and hydrocracking.
e.g.
A typical reaction:
catalyst
C16H34 -> C8H18 + C8H16
The cracking reaction yields petrol, LPG, unsaturated olefin compounds, cracked gas oils, a liquid residue called cycle oil, light gases and a solid coke residue. Cycle oil is recycled to cause further breakdown and the coke, which forms a layer on the catalyst, is removed by burning. The other products are passed through a fractionator to be separated and separately processed.
Fluid catalytic cracking uses a catalyst in the form of a very fine powder which flows like a liquid when agitated by steam, air or vapour. Feedstock entering the process immediately meets a stream of very hot catalyst and vaporises. The resulting vapours keep the catalyst fluidised as it passes into the reactor, where the cracking takes place and where it is fluidised by the hydrocarbon vapour. The catalyst next passes to a steam stripping section where most of the volatile hydrocarbons are removed. It then passes to a regenerator vessel where it is fluidised by a mixture of air and the products of combustion which are produced as the coke on the catalyst is burnt off. The catalyst then flows back to the reactor. The catalyst thus undergoes a continuous circulation between the reactor, stripper and regenerator sections.
The catalyst is usually a mixture of aluminium oxide and silica. Most recently, the introduction of synthetic zeolite catalysts has allowed much shorter reaction times and improved yields and octane numbers of the cracked gasolines.
Thermal cracking uses heat to break down the residue from vacuum distillation. The lighter elements produced from this process can be made into distillate fuels and petrol. Cracked gases are converted to petrol blending components by alkylation or polymerisation. Naphtha is upgraded to high quality petrol by reforming. Gas oil can be used as diesel fuel or can be converted to petrol by hydrocracking. The heavy residue is converted into residual oil or coke which is used in the manufacture of electrodes, graphite and carbides.
This process is the oldest technology and is not used in Australia.
Hydrocracking can increase the yield of petrol components, as well as being used to produce light distillates. It produces no residues, only light oils. Hydrocracking is catalytic cracking in the presence of hydrogen. The extra hydrogen saturates, or hydrogenates, the chemical bonds of the cracked hydrocarbons and creates isomers with the desired characteristics. Hydrocracking is also a treating process, because the hydrogen combines with contaminants such as sulphur and nitrogen, allowing them to be removed.
Gas oil feed is mixed with hydrogen, heated, and sent to a reactor vessel with a fixed bed catalyst, where cracking and hydrogenation take place. Products are sent to a fractionator to be separated. The hydrogen is recycled. Residue from this reaction is mixed again with hydrogen, reheated, and sent to a second reactor for further cracking under higher temperatures and pressures.
In addition to cracked naphtha for making petrol, hydrocracking yields light gases useful for refinery fuel, or alkylation as well as components for high quality fuel oils, lube oils and petrochemical feedstocks.
Following the cracking processes it is necessary to build or rearrange some of the lighter hydrocarbon molecules into high quality petrol or jet fuel blending components or into petrochemicals. The former can be achieved by several chemical process such as alkylation and isomerisation.
Alkylation
Olefins such as propylene and butylene are produced by catalytic and thermal cracking. Alkylation refers to the chemical bonding of these light molecules with isobutane to form larger branched-chain molecules (isoparaffins) that make high octane petrol.
Olefins and isobutane are mixed with an acid catalyst and cooled. They react to form alkylate, plus some normal butane, isobutane and propane. The resulting liquid is neutralised and separated in a series of distillation columns. Isobutane is recycled as feed and butane and propane sold as liquid petroleum gas (LPG).
e.g.
catalyst
isobutane +butylene -> isooctane
C4H10 + C4H8 -> C8H18
Isomerisation
Isomerisation refers to chemical rearrangement of straight-chain hydrocarbons (paraffins), so that they contain branches attached to the main chain (isoparaffins). This is done for two reasons:
they create extra isobutane feed for alkylation
they improve the octane of straight run pentanes and hexanes and hence make them into better petrol blending components.
Isomerisation is achieved by mixing normal butane with a little hydrogen and chloride and allowed to react in the presence of a catalyst to form isobutane, plus a small amount of normal butane and some lighter gases. Products are separated in a fractionator. The lighter gases are used as refinery fuel and the butane recycled as feed.
Pentanes and hexanes are the lighter components of petrol. Isomerisation can be used to improve petrol quality by converting these hydrocarbons to higher octane isomers. The process is the same as for butane isomerisation.
Polymerisation
Under pressure and temperature, over an acidic catalyst, light unsaturated hydrocarbon molecules react and combine with each other to form larger hydrocarbon molecules. Such process can be used to react butenes (olefin molecules with four carbon atoms) with iso-butane (branched paraffin molecules, or isoparaffins, with four carbon atoms) to obtain a high octane olefinic petrol blending component called polymer gasoline.
Hydrotreating and sulphur plants
A number of contaminants are found in crude oil. As the fractions travel through the refinery processing units, these impurities can damage the equipment, the catalysts and the quality of the products. There are also legal limits on the contents of some impurities, like sulphur, in products.
Hydrotreating is one way of removing many of the contaminants from many of the intermediate or final products. In the hydrotreating process, the entering feedstock is mixed with hydrogen and heated to 300 - 380oC. The oil combined with the hydrogen then enters a reactor loaded with a catalyst which promotes several reactions:
hydrogen combines with sulphur to form hydrogen sulphide (H2S)
nitrogen compounds are converted to ammonia
any metals contained in the oil are deposited on the catalyst
some of the olefins, aromatics or naphthenes become saturated with hydrogen to become paraffins and some cracking takes place, causing the creation of some methane, ethane, propane and butanes.
Sulphur recovery plants
The hydrogen sulphide created from hydrotreating is a toxic gas that needs further treatment. The usual process involves two steps:
the removal of the hydrogen sulphide gas from the hydrocarbon stream
the conversion of hydrogen sulphide to elemental sulphur, a non-toxic and useful chemical.
Solvent extraction, using a solution of diethanolamine (DEA) dissolved in water, is applied to separate the hydrogen sulphide gas from the process stream. The hydrocarbon gas stream containing the hydrogen sulphide is bubbled through a solution of diethanolamine solution (DEA) under high pressure, such that the hydrogen sulphide gas dissolves in the DEA. The DEA and hydrogen mixture is the heated at a low pressure and the dissolved hydrogen sulphide is released as a concentrated gas stream which is sent to another plant for conversion into sulphur.
Conversion of the concentrated hydrogen sulphide gas into sulphur occurs in two stages.
Combustion of part of the H2S stream in a furnace, producing sulphur dioxide (SO2) water (H2O) and sulphur (S).
2H2S + 2O2 -> SO2 + S + 2H2O
Reaction of the remainder of the H2S with the combustion products in the presence of a catalyst. The H2S reacts with the SO2 to form sulphur.
2H2S + 2O2 -> 3S + 2H2O
As the reaction products are cooled the sulphur drops out of the reaction vessel in a molten state. Sulphur can be stored and shipped in either a molten or solid state.
Click here to view a flow chart of a refinery .
Refineries and the environment
Air, water and land can all be affected by refinery operations. Refineries are well aware of their responsibility to the community and employ a variety of processes to safeguard the environment.
The processes described below are those used by the Shell refinery at Geelong in Victoria, but all refineries employ similar techniques in managing the environmental aspects of refining.
Air
Preserving air quality around a refinery involves controlling the following emissions:
sulphur oxides
hydrocarbon vapours
smoke
smells
Sulphur enters the refinery in crude oil feed. Gippsland and most other Australian crude oils have a low sulphur content but other crude's may contain up to 5 per cent sulphur. To deal with this refineries incorporate a sulphur recovery unit which operates on the principles described above.
Many of the products used in a refinery produce hydrocarbon vapours. The escape of vapours to atmosphere are prevented by various means. Floating roofs are installed in tanks to prevent evaporation and so that there is no space for vapour to gather in the tanks. Where floating roofs cannot be used, the vapours from the tanks are collected in a vapour recovery system and absorbed back into the product stream. In addition, pumps and valves are routinely checked for vapour emissions and repaired if a leakage is found.
Smoke is formed when the burning mixture contains insufficient oxygen or is not sufficiently mixed. Modern furnace control systems prevent this from happening during normal operation.
Smells are the most difficult emission to control and the easiest to detect. Refinery smells are generally associated with compounds containing sulphur, where even tiny losses are sufficient to cause a noticeable odour.
Water
Aqueous effluent's consist of cooling water, surface water and process water.
The majority of the water discharged from the refinery has been used for cooling the various process streams. The cooling water does not actually come into contact with the process material and so has very little contamination. The cooling water passes through large "interceptors" which separate any oil from minute leaks etc., prior to discharge. The cooling water system at Geelong Refinery is a once-through system with no recirculation.
Rainwater falling on the refinery site must be treated before discharge to ensure no oily material washed off process equipment leaves the refinery. This is done first by passing the water through smaller "plant oil catchers", which each treat rainwater from separate areas on the site, and then all the streams pass to large "interceptors" similar to those used for cooling water. The rainwater from the production areas is further treated in a Dissolved Air Flotation (DAF) unit. This unit cleans the water by using a flocculation agent to collect any remaining particles or oil droplets and floating the resulting flock to the surface with millions of tiny air bubbles. At the surface the flock is skimmed off and the clean water discharged.
Process water has actually come into contact with the process streams and so can contain significant contamination. This water is treated in the "sour water treater" where the contaminants (mostly ammonia and hydrogen sulphide) are removed and then recovered or destroyed in a downstream plant. The process water, when treated in this way, can be reused in parts of the refinery and discharged through the process area rainwater treatment system and the DAF unit.
Any treated process water that is not reused is discharged as Trade Waste to the sewerage system. This trade waste also includes the effluent from the refinery sewage treatment plant and a portion of treated water from the DAF unit.
As most refineries import and export many feed materials and products by ship, the refinery and harbour authorities are prepared for spillage from the ship or pier. In the event of such a spill, equipment is always on standby at the refinery and it is supported by the facilities of the Australian Marine Oil Spill Centre at Geelong, Victoria.
Land
The refinery safeguards the land environment by ensuring the appropriate disposal of all wastes.
Within the refinery, all hydrocarbon wastes are recycled through the refinery slops system. This system consists of a network of collection pipes and a series of dewatering tanks. The recovered hydrocarbon is reprocessed through the distillation units.
Wastes that cannot be reprocessed are either recycled to manufacturers (e.g. some spent catalysts can be reprocessed), disposed of in EPA-approved facilities off-site, or chemically treated on-site to form inert materials which can be disposed to land-fill within the refinery.
Waste movements within the refinery require a "Process liquid, Sludge and Solid waste disposal permit". Wastes that go off-site must have an EPA "Waste Transport Permit".
Friday, August 14, 2009
Composting of bio degradeable waste
A biodegradable material is capable of being completely broken down under the action of microorganisms into carbon dioxide, water and biomass. It may take a very long time for some material to biodegrade depending on its environment (e.g. wood in an arid area versus paper in water), but it ultimately breaks down completely. Many contaminating materials not dealt with in common composting are in fact "biodegradeable", and may be dealt with via bioremediation, or other special composting approaches.
Stable bedding after shredding and three weeks of hot aerobic composting.A compostable material biodegrades substantially under specific composting conditions. It is metabolized by the microorganisms, being incorporated into the organisms or converted into humus. The size of the material is a factor in determining compostability, and mechanical particle size reduction can speed the process. Large pieces of hardwood may not be compostable under a specific set of composting conditions, whereas sawdust of the same type of wood may be. Some biodegradeable materials are only compostable under very specific conditions, usually with an industrial process.
Contents [hide]
1 Importance
2 Materials
3 Approaches
3.1 Active (aerobic)
3.2 Passive (anaerobic)
4 In nature
5 Vermicomposting
6 Industrial systems
7 Agriculture
8 See also
9 References
10 External links
[edit] Importance
Composting upcycles organic kitchen and yard waste and manures into an extremely useful humus-like, soil end product, permitting the return of vital organic matter, nutrients, and particularly bacteria, that are vital to plant nutrition to the soil. Managed aerobic composting arranges environmental conditions so they are optimal for the natural processes to take place. There is a popular expression: "compost happens", but it is helpful to engineer the best possible circumstances for large amounts of organic waste to decompose quickly and efficiently, with the greatest conservation of useful nutrients and mass. Uncontrolled composting is when compost "happens", and although that may be functional in some circumstances, as with forest floor detritus, a neglected heap of kitchen and yard wastes will more likely result in "smells happen", or "rodents happen" long before useful compost does.
Long used in subsistence farming and home gardening for creating garden-ready soil, composting is becoming increasingly important and better understood as a tool for reducing municipal solid waste,[4] and reducing the amount of green waste going into landfills. The decomposition of organic material sent to landfills is a principal cause of methane, an important greenhouse gas, making reduction of organic waste being landfilled a key element in the fight against climate change. In suburban and rural areas, much of the organic waste could be removed from the waste stream by promoting home composting, where consumers compost their yard waste and kitchen scraps on their own land, regardless of whether the material is ever actively re-used as "soil".[5] In urban areas with dwellings predominantly lacking individual yard space, there are indoor small scale composting alternatives, such as vermicomposting and bokashi composting.[6]
[edit] Materials
Posters for compost education (European)Composting organisms require four equally important things to work effectively:
Carbon ("C" or carbohydrates), for energy - the microbial oxidation of carbon produces the heat.
High carbon materials tend to be brown and dry.
Nitrogen ("N" or protein), to grow and reproduce more organisms to oxidize the carbon.
High nitrogen materials tend to be green (or colorful, like fruits and vegetables) and wet.[7]
Oxygen, for oxidizing the carbon, the decomposition process.
Water, in the right amounts to maintain activity without causing anaerobic conditions.
Certain ratios of these elements will provide beneficial bacteria with the nutrients to work at a rate that will heat up the pile. In that process much water will be released as vapor ("steam"), and the oxygen will be quickly depleted, explaining the need to actively manage the pile. The hotter the pile gets, the more often added air and water is necessary; the air/water balance is critical to maintaining high temperatures until the materials are broken down. At the same time, too much air or water also slows the process, as does too much C (or too little N).
The most efficient composting occurs with a C:N mix of about 30 to 1. All organics have both carbon and nitrogen, but amounts vary widely, with characteristics noted above (dry/wet, brown/green).[8] Fresh grass clippings have an average ratio of about 15 to 1 and dry autumn leaves about 50 to 1 depending on species. Mixing equal parts by volume approximates the ideal C:N range. Few individual situations will provide the ideal mix of materials at any point in time - in this respect, home composting is like horseshoes, perfect is great, but close still works. Observation of amounts, and consideration of different materials[9] as a pile is built over time can quickly achieve a workable technique for the individual situation.
Home compost barrel in the Escuela Barreales, Chile.Ingredients that are primarily carbon include:
Dry, straw-type material, such as cereal straws and corn stalks
Dry leaves (best shredded, as with a rotary mower, to prevent matting)
Wood, as coarse or fine (may compact) sawdust, or ground wood waste
Paper, corrugated cardboard, box board, and office paper or newsprint (soy-based inks)
Ingredients with relatively high nitrogen content include:
Green plant material, like crop residues, hay (especially alfalfa), grass clippings and weeds.
Manure from poultry, and herbivorous animals such as horses, cows and llamas.
Kitchen waste - fruit and vegetable cooked waste and trimmings, juicing-pulp residue, tea and coffee grounds.
For "back yard" composting, mixing the materials as they are added increases the rate of decomposition, as does reduced particle size (ie, chopped, shredded), or materials can be added in alternating layers, about 15 centimeters (6 in) thick. Keeping a carbon "cache" handy to the pile for covering and mixing with fresh wet additions (lawn clippings, kitchen scraps) is simplest. Special additions or activators are not necessary, although some sprinklings of good garden loam as a first pile is built will aid more rapid working by inoculating it with beneficial soil bacteria, and some of the material from the first finished batch can be used in the subsequent mixes. Agricultural lime is not necessary - the bacteria prefer a slightly acidic pH, and their processing invariably results in a near-neutral product.[10] Seaweed meal, rock dust or rock flour, and other trace element amendments are best added to the finished compost, or directly to the garden.
[edit] Approaches
[edit] Active (aerobic)
An active compost heap, steaming on a cool morning. The heap is kept warm by the exothermic action of the bacteria as they decompose the organic matter.Hot thermophilic composting is essential with some materials, such as meat and other animal products, dairy products, eggs, grease, cooking oil, manure of non-herbivores, and residuals from the treatment of wastewater, in order to kill pathogens; but these materials are not generally recommended in home composting because of the likelihood of creating odors and attracting rodents. Human waste can be composted by industrial methods as well as composting toilets. When high temperatures are reached, the resulting compost can be safely used for agricultural or horticultural purposes, providing local health regulations are met. Humanure fertilizer (as opposed to night soil) is used throughout the developing world and is becoming more accepted as a garden amendment in the developed world.
Hot, aerobic composting is conducted at close to the ideal conditions noted above, allowing thermophilic bacteria to thrive. These aerobic bacteria break down material faster, producing less odor, fewer pathogens, and less greenhouse gas than cool, uncontrolled, or accidental anaerobic methods. Commercial scale composting operations actively control the composting conditions (C:N ration, moisture level and air), usually in a closed environment (in-vessel composting, tunnel composting or aerated static pile composting), where air is fan forced through the mass, and moisture added with sprayers, or conserved via the enclosure, with computer monitored probes detecting conditions.
In Thailand an aerated static pile system is in use by farmer groups at over 400 sites. The process needs only 30 days to finish without manual turning, with 10 metric tons of compost produced per month. A 38 centimetres (15 in) squirrel-cage blower with 2.2 kilowatts (3.0 hp) motor is used to force air through 10 covered static piles of compost twice a day. The raw materials consist of agricultural wastes and animal manure in the ratio of 3:1 by volume.[11]
High temperatures destroy insects, larvae, and weed seeds, but no compost will be totally sterilized by high temperatures alone. In a hot compost where the temperature exceeds 55 °C (131 °F) for several days, the ability of most organisms to survive is compromised, and there are temperature standards[12] set by various regulating authorities for commercial products[13] Nevertheless, many organisms in nature can survive extreme temperatures, including extremophiles such as Thermus thermophilus which play an important role in thermogenic composting,[14] as well as pathogens such as Clostridium. The necessary second stage of hot composting is maturation, a period allowing the dissipation of any phyto-toxins[15] remaining from the process or contaminating ingredients (eg: chemical residues), and achieving a state of nutrient stability (low C:N ratio) that will not have an impact on Nitrogen availability in the receiving soil.[16]
An alternative to manual turning, the "Wing Ding" compost aeratorFor backyard composters, carbon and nitrogen ratios in various ingredients and the calculations required to get the ideal mixture can be intimidating, so rules of thumb exist for approximating it by ingredient types and condition, as mentioned in Materials above. If the pile is built in a short period, and has a good mix of materials (C:N) and a coarse structure, with about 50% moisture ("like a squeezed out sponge"), the temperature should rise within days to as high as 60 °C (140 °F). When the temperature begins to fall, more air is needed, usually added by turning the pile or using an agitating tool, and moisture may be needed at the same time. Turning or other aeration is usually needed about every 6–10 days to maintain the highest heat levels until the material is fairly uniformly broken down to unrecognizability, and temperatures no longer rebound. A pile that has been maintained at peak temperatures may be ready for maturing in as little as 30 days. Another 30–60 days maturing should suffice to allow passing the "germination test".[17]
To achieve thermophilic decomposition, a compost bin is best about 1 cubic metre (1.3 cu yd), or 1 metre (3 ft) wide, 1 metre (3 ft) tall, and as long as desired for windrow composting. This provides enough insulating mass to build up heat but also allows oxygen infiltration. The center of the pile heats up the most, so regular turning/mixing is needed for insuring all material spends some time in the hottest area. When turning the pile results in no further temperature rise, the active aerobic phase is complete, and the mass may be turned out to a maturing pile. When the matured material has a dark brown crumbly appearance and the smell of rich damp earth, it is ready to use.
Turning a home compost binThe natural sequence of the decomposition community involved will be:
0-15 °C (32-59 °F) - psychrophiles predominate, beginning the heating process as they multiply
15-40 °C (60-104 °F) - mesophiles take over, psychrophiles die off or are relegated to the borders
40-70 °C (105-160 °F) - thermophiles work at their peak, including consuming many other bacteria
At the lower temperatures and around the borders, there will also be various fungal activity, as well as larger organisms, getting their share - a very dry, cooler pile may be attractive to ants, and gastropods may visit very wet piles. As the temperature returns to ambient at the end of the process, the sequence reverses, including new organisms that prefer the more degraded materials. Added heat and pile insulation may be useful in the coldest weather, but is not ordinarily necessary, and is not desirable if it interferes with aeration or natural convective evaporation. Keeping the top dry and burying fresh additions in the center of a pile will be effective during winter conditions until heating resumes in spring.
[edit] Passive (anaerobic)
Cool or ambient temperature composting, when the level of physical intervention is minimal, usually results in temperatures never reaching above 30°C (86°F). It is slower but effective, and is the more common type of composting in domestic gardening. Such composting systems may be in open or closed containers of wood or plastic, or in open exposed piles. Kitchen scraps are put in the garden compost bin and left untended. This scrap bin can have a very high water content which reduces aeration, and may become odorous. To improve drainage and airflow, and reduce odor, carbon-rich materials, or 'browns', such as wood chips, shredded bark, leaves, or twigs may be added to mix and cover each wet addition, or holes made occasionally in the pile. The amount of attention may vary from none through occasional to "regular".
[edit] In nature
An unusual form of composting in nature is seen in the case of the mound-builders (megapodes) of the Australasian region. These Megapodes are fowl-sized birds famous for building nests in the form of compost heaps containing organic litter, in which they incubate their eggs. The male birds work assiduously to maintain the correct incubation temperatures, by adding and removing litter from the compost pile.
Forest floor detritus is the natural fertilizing material in temperate forests. Soil dwelling organisms slowly decompose the continuously deposited litter from below, returning the nutrients to the soil for bacterial conversion to forms useful to the native vegation. This is a natural form of mulching or sheet composting. While some may be tempted to gather this rich, partially decomposed litter for use in a home garden, it is best left to the use of the forest.
[edit] Vermicomposting
Worm composting or vermicomposting is a method using Red Wiggler worms in a container to process kitchen waste. Moistened high-carbon bedding such as shredded paper is used as a base to which the food waste is added, and the worms and micro-organisms convert the materials to rich compost called worm castings, a nutrient and microbially rich material. Worm composting can be done indoors, allowing year-round composting, and providing apartment dwellers with a means of recycling food waste.
[edit] Industrial systems
Industrial composting systems are increasingly being installed as a waste management alternative to landfills, along with other advanced waste processing systems. Mechanical sorting of mixed waste streams combined with anaerobic digestion or in-vessel composting, is called mechanical biological treatment, increasingly used in developed countries due to regulations controlling the amount of organic matter allowed in landfills. Treating biodegradable waste before it enters a landfill reduces global warming from fugitive methane; untreated waste breaks down anaerobically in a landfill, producing landfill gas that contains methane, a potent greenhouse gas.
Large-scale composting systems are used by many urban centers around the world. Co-composting is a technique which combines solid waste with de-watered biosolids, although difficulties controlling inert and plastic contamination from Municipal solid waste makes this approach less attractive. The world's largest MSW co-composter is the Edmonton Composting Facility in Edmonton, Alberta, Canada, which turns 220,000 tonnes of residential solid waste and 22,500 dry tonnes of biosolids per year into 80,000 tonnes of compost. The facility is 38,690 meters2 (416,500 ft2), equivalent to 4½ Canadian football fields, and the operating structure is the largest stainless steel building in North America, the size of 14 NHL rinks.[18]
[edit] Agriculture
Compost is an important source of nutrients commonly used in modern agriculture. Through steaming compost can be sanitized and prepared for further use.
Friday, July 3, 2009
INTERVIEW FAQs and their answers
1. Tell me something about your self
This is usually the first question you face in an interview. The purpose of this question is to:
a) Put the candidate at ease and b) Initiate a discussion.
The answer to this question should cover a little information about your work experience, educational qualifications and family background. Your answer to this question can help you take the interview in whichever direction you want. The key to this is to put a full stop to your answer at the right place to provoke the second question you want.
2. Why have you applied for this job?
A good way to answer this question in practical way is to talk about the requirements of the job, relate your skills and experience to it. To do this, you need to carefully go through the job requirements and ask yourself how your skills fit into the requirement.
Your CV will be your best companion to identify your skills and match them with the requirements.
It won't be much helpful to talk about the career, progression and the challenges this job offers.
3. Why do you want to leave your present job or why did you leave your last job?
You can switch jobs for numerous reasons which can be you are not happy with your profile, you don't get well along with your boss, the salary they pay is less etc. The key to this question lies in 3Es.
When asked this question, you can simply say : for better prospects in terms of experience, exposure and earnings.
In current market situation, lay offs are common everywhere and owing to them people are looking out for jobs. If this is the case with you, chose your words carefully so that you do not leave an impression that it was only you who was laid off.
You can say something like: As you know, in the current economic situation, almost everybody is trying to cut costs. A lot of restructuring has been happening in my company also over the last X months and finally "Y" jobs were made redundant. One of them was mine. Leave the answer here with out giving too much importance to the fact that you were "laid off". It can happen with anyone and need not necessarily be your fault.
4. What is your greatest strength?
Take this question as "Why should we hire you?"
Sell them a strength or two which they are ready to buy. It can be anything directly related to the requirements of job under discussion.
Identify the qualities the job needs a person to have and how your skills fit into them. To do this you will need to:
· Understand the requirements of the job
· Identify your skills and match the two
5. What is your greatest weakness?
There are three ways to answer this question depending on the environment in which the discussion is going on. Understand the environment and use one of them:
Use your sense of humor and say something cool like "movies". This has to be accompanied by a right body language. This method would work if the discussion is going on in a light environment.
If you need to answer this question seriously offer a weakness which doesn't relate to the job immediately under discussion. It would be foolish to say that "I am slow at taking notes or typing" if you are applying for a secretarial job.
If you have applied for a job in marketing and you do not know cooking properly, you can say something like I have been using a microwave since last two years but I still can't bake a good cake.
Turn your weakness into your strength: frame your words in a way that they convey, others accuse you of having this weakness but you actually treat it as your strength. For example: my friends accuse me of being too people friendly but I think being in marketing I need to develop a good social network and I think this people friendliness takes me a long way.
6. You have switched many jobs, why?
Switching many jobs makes you a job hopper and gives an impression that the candidate is unreliable.
To answer this question, you can say something like to broaden your experience.
7. You do not have all the experience we are seeking for this position
It is not necessary that the candidate who knows everything about the job would be the best fit for the job. It is the person's willingness to learn which matters more.
Understand the job requirements properly and if you meet most of the requirements, you can say that you meet most of the requirements and you will be happy to learn whatever you don't know.
Moreover, there might be some new things in the job in future and your willingness to learn will help you do the job well. You can accompany this with an example where you learnt new things and implemented them successfully in the past.
8. Where do you see yourself five years from now?
The purpose of this question is to understand how ambitious the candidate is.
You can say something like, I see myself in a more responsible position where I can make important decisions for the company and am treated as an asset. I hope I can get both these things in this job.
9. Your expected salary?
This is the trickiest question in the interview to answer.
Try not to be the first one to throw a figure in the court. Ask the interviewer, what is it that they offer for a position like this? Know your baseline below which you can't go and try to negotiate above that. Also, make sure that you know your market value so that you do not try to negotiate too much and finally lose the opportunity.
If you have to give a figure, mention a range rather than the exact figure and don't keep the range too broad. If you offer a very broad range, you will be offered something towards the lower end. Say something like: I'll be comfortable with something around mid-forties.
10. Do you want to ask us something about the company?
Don't come out like a dumb when you are given an opportunity to ask questions.
Research a bit about the company and ask some intelligent questions like the expansion plan, opportunity for you to grow in the company, anything for which the company has been in news recently etc
Thursday, June 11, 2009
Biotechnology
It covers a wide variety of subjects like Genetics, Biochemistry, Microbiology, Immunology, Virology, Chemistry and Engineering. It also has tight links and relationships with many other subjects like Health and Medicine, Agriculture and Animal Husbandry, Cropping system and Crop Management, Ecology, Cell Biology, Soil Science and Soil Conservation, Bio-statistics, Plant Physiology, Seed Technology and the like. Biotechnology is the use of living things, especially cells and bacteria in industrial process. With demand for biotechnologists growing prospects in this industry are increasing.
Types of courses
5 year integrated M.Sc/ M.Tech courses
Today a number of colleges offer Bachelors programmes in biotechnology. Since the course demands diverse skill sets, a strong disciplinary training in various basic sciences, would, in my opinion, add more value in the long run than a B.Sc (Biotech) programme. Unless of course, one opts for a five year integrated MSc/ MTech programme offered by institutions like IITs.
M.Sc (Biotechnology)
This is a very popular course where any graduate in biology or related sciences is eligible to apply. There are two major entrance exams for the course. The All India Biotechnology Entrance test conducted by JNU for admission to about 500 odd seats in the 32 university departments is the first major one. IITs admit students through a Joint Admissions Test for IITs. Most good private sector universities have their own independent examinations. While public sector schools are subsidized, and have very low fees, the private sector ones charge substantially higher fees.
This is a recent entrant in to the pantheon of famed MBA degrees. It normally requires a candidate to have a bachelor's degree in biological or related sciences. The degree might enable one to move into business functions in a biotech company with greater ease, since one has developed a certain understanding of the sector even before one has joined it. Institutions like NMIMS, Pune University offer such degrees.
PhD (Biotechnology)
If it is a career in research, that you're are seeking, then a PhD in biotechnology is a must. Most of the institutions mentioned above also offer you the option to pursue research studies. A valid GATE score (for engineering graduates) or a high score in the UGC-JRF or a CSIR or ICMR fellowship would ease your entry and also provide you with stable fellowships. Most of the institutes offer part time teaching/ research assistance to candidates unable to obtain a fellowship. Many students try and obtain their PhD from foreign universities as well.
Some of the institutions in India like the IISc also offer an integrated 5 year PhD programme after a BSc.
MBA (Biotechnology)
This is a recent entrant in to the pantheon of famed MBA degrees. It normally requires a candidate to have a bachelor's degree in biological or related sciences. The degree might enable one to move into business functions in a biotech company with greater ease, since one has developed a certain understanding of the sector even before one has joined it. Institutions like NMIMS, Pune University offer such degrees.
Saturday, April 4, 2009
Cracking in process industries.
Oil refinery cracking processes allow the production of "light" products such as LPG and gasoline from heavier crude oil distillation fractions such as gas oils and residues. Fluid Catalytic Cracking (FCC) produces a high yield of gasoline and LPG while hydrocracking is a major source of jet fuel, diesel, naphtha and LPG.
Thermal cracking is currently used to "upgrade" very heavy fractions ("upgrading", "visbreaking"), or to produce light fractions or distillates, burner fuel and/or petroleum coke. Two extremes of the thermal cracking in terms of product range are represented by the high-temperature process called "steam cracking" or pyrolysis (ca. 750 to 900 °C or more) which produces valuable ethylene and other feedstocks for the petrochemical industry, and the milder-temperature delayed coking (ca. 500 °C) which can produce, under the right conditions, valuable needle coke, a highly crystalline petroleum coke used in the production of electrodes for the steeland aluminium industries.
Fluid catalytic cracking
Main article: Fluid catalytic cracking
Fluid catalytic cracking is a commonly used process and a modern oil refinery will typically include a cat cracker, particularly at refineries in the USA due to the high demand for gasoline.The process was first used in around 1942 and employs a powdered catalyst. During the Second World War, it provided Allied Forces with plentiful supplies of gasoline and artificial rubber that contrasted with the penury suffered by the Axis Forces. Initial process implementations were based on a low activity alumina catalyst and a reactor where the catalyst particles were suspended in a rising flow of feed hydrocarbons in a fluidized bed.
Alumina-catalyzed cracking systems are still in use in high school and university laboratories in experiments concerning alkanes and alkenes. The catalyst is usually obtained by crushing pumice stones, which contain mainly aluminium oxide and silica into small, porous pieces. In the laboratory, aluminium oxide (or porous pot) must be heated.
In newer designs, cracking takes place using a very active zeolite-based catalyst in a short-contact time vertical or upward sloped pipe called the "riser". Pre-heated feed is sprayed into the base of the riser via feed nozzles where it contacts extremely hot fluidized catalyst at 1230 to 1400 °F (665 to 760 °C). The hot catalyst vaporizes the feed and catalyzes the cracking reactions that break down the high molecular weight oil into lighter components including LPG, gasoline, and diesel. The catalyst-hydrocarbon mixture flows upward through the riser for just a few seconds and then the mixture is separated via cyclones. The catalyst-free hydrocarbons are routed to a main fractionator for separation into fuel gas, LPG, gasoline, naphtha, light cycle oils used in diesel and jet fuel, and heavy fuel oil.
During the trip up the riser, the cracking catalyst is "spent" by reactions which deposit coke on the catalyst and greatly reduce activity and selectivity. The "spent" catalyst is disengaged from the cracked hydrocarbon vapors and sent to a stripper where it is contacted with steam to remove hydrocarbons remaining in the catalyst pores. The "spent" catalyst then flows into a fluidized-bed regenerator where air (or in some cases air plus oxygen) is used to burn off the coke to restore catalyst activity and also provide the necessary heat for the next reaction cycle, cracking being an endothermic reaction. The "regenerated" catalyst then flows to the base of the riser, repeating the cycle.
The gasoline produced in the FCC unit has an elevated octane rating but is less chemically stable compared to other gasoline components due to its olefinic profile. Olefins in gasoline are responsible for the formation of polymeric deposits in storage tanks, fuel ducts and injectors. The FCC LPG is an important source of C3-C4 olefins and isobutane that are essential feeds for the alkylation process and the production of polymers such as polypropylene.
[edit] Hydrocracking
In 1920 a plant for the commercial hydrogenation of brown coal is commissioned at Leuna in Germany[8].
Hydrocracking is a catalytic cracking process assisted by the presence of an elevated partial pressure of hydrogen gas. Similar to the hydrotreater, the function of hydrogen is the purification of the hydrocarbon stream from sulfur and nitrogen hetero-atoms.
The products of this process are saturated hydrocarbons; depending on the reaction conditions (temperature, pressure, catalyst activity) these products range from ethane, LPG to heavier hydrocarbons comprising mostly of isoparaffins. Hydrocracking is normally facilitated by a bi functional catalyst that is capable of rearranging and breaking hydrocarbon chains as well as adding hydrogen to aromatics and olefins to produce naphthenes and alkanes.
Major products from hydrocracking are jet fuel and diesel, while also relatively high octane rating gasoline fractions and LPG are produced. All these products have a very low content of sulfur and other contaminants.
It is very common in India, Europe and Asia because those regions have high demand for diesel and kerosene. In the US, Fluid Catalytic Cracking is more common because the demand for gasoline is higher.
[edit] Steam cracking
Steam cracking is a petrochemical process in which saturated hydrocarbons are broken down into smaller, often unsaturated, hydrocarbons. It is the principal industrial method for producing the lighter alkenes (or commonly olefins), including ethene (or ethylene) and propene (or propylene).
In steam cracking, a gaseous or liquid hydrocarbon feed like Naphtha, LPG or Ethane is diluted with steam and then briefly heated in a furnace (obviously without the presence of oxygen). Typically, the reaction temperature is very high —around 850°C—but the reaction is only allowed to take place very briefly. In modern cracking furnaces, the residence time is even reduced to milliseconds (resulting in gas velocities reaching speeds beyond the speed of sound) in order to improve the yield of desired products. After the cracking temperature has been reached, the gas is quickly quenched to stop the reaction in a transfer line heat exchanger.
The products produced in the reaction depend on the composition of the feed, the hydrocarbon to steam ratio and on the cracking temperature and furnace residence time.
Light hydrocarbon feeds (such as ethane, LPGs or light naphthas) give product streams rich in the lighter alkenes, including ethylene, propylene, and butadiene. Heavier hydrocarbon (full range and heavy naphthas as well as other refinery products) feeds give some of these, but also give products rich in aromatic hydrocarbons and hydrocarbons suitable for inclusion in gasoline or fuel oil. The higher cracking temperature (also referred to as severity) favours the production of ethene and benzene, whereas lower severity produces relatively higher amounts of propene, C4-hydrocarbons and liquid products.
The process also results in the slow deposition of coke, a form of carbon, on the reactor walls. This degrades the efficiency of the reactor, so reaction conditions are designed to minimize this. Nonetheless, a steam cracking furnace can usually only run for a few months at a time between de-cokings. Decokes require the furnace to be isolated from the process and then a flow of steam or a steam/air mixture is passed through the furnace coils . This converts the hard solid carbon layer to carbon monoxide and carbon dioxide. Once this reaction is complete, the furnace can be returned to service.
[edit] Chemistry
"Cracking" breaks larger molecules into smaller ones. This can be done with a thermic or catalytic method.
The thermal cracking process follows a homolytic mechanism, that is, bonds break symmetrically and thus pairs of free radicals are formed.
The catalytic cracking process involves the presence of acid catalysts (usually solid acids such as silica-alumina and zeolites) which promote a heterolytic (asymmetric) breakage of bonds yielding pairs of ions of opposite charges, usually a carbocation and the very unstable hydride anion. Carbon-localized free radicals and cations are both highly unstable and undergo processes of chain rearrangement, C-C scission in position beta (i.e., cracking) and intra- and intermolecular hydrogen transfer or hydride transfer. In both types of processes, the corresponding reactive intermediates (radicals, ions) are permanently regenerated, and thus they proceed by a self-propagating chain mechanism. The chain of reactions is eventually terminated by radical or ion recombination.
[edit] Thermal cracking
William Merriam Burton developed one of the earliest thermal cracking processes in 1912 which operated at 700-750 °F (370-400 °C) and an absolute pressure of 90 psia (620 kPa) and was known as the Burton process. Shortly thereafter, in 1921, C.P. Dubbs, an employee of the Universal Oil Products Company, developed a somewhat more advanced thermal cracking process which operated at 750-860 °F (400-460 °C) and was known as the Dubbs process.[9] The Dubbs process was used extensively by many refineries until the early 1940's when catalytic cracking came into use.
Modern high-pressure thermal cracking operates at absolute pressures of about 7,000 kPa. An overall process of disproportionation can be observed, where "light", hydrogen-rich products are formed at the expense of heavier molecules which condense and are depleted of hydrogen. The actual reaction is known as homolytic fission and produces alkenes, which are the basis for the economically important production of polymers.
A large number of chemical reactions take place during steam cracking, most of them based on free radicals. Computer simulations aimed at modeling what takes place during steam cracking have included hundreds or even thousands of reactions in their models. The main reactions that take place include:
Initiation reactions, where a single molecule breaks apart into two free radicals. Only a small fraction of the feed molecules actually undergo initiation, but these reactions are necessary to produce the free radicals that drive the rest of the reactions. In steam cracking, initiation usually involves breaking a chemical bond between two carbon atoms, rather than the bond between a carbon and a hydrogen atom.
CH3CH3 → 2 CH3•
Hydrogen abstraction, where a free radical removes a hydrogen atom from another molecule, turning the second molecule into a free radical.
CH3• + CH3CH3 → CH4 + CH3CH2•
Radical decomposition, where a free radical breaks apart into two molecules, one an alkene, the other a free radical. This is the process that results in the alkene products of steam cracking.
CH3CH2• → CH2=CH2 + H•
Radical addition, the reverse of radical decomposition, in which a radical reacts with an alkene to form a single, larger free radical. These processes are involved in forming the aromatic products that result when heavier feedstocks are used.
CH3CH2• + CH2=CH2 → CH3CH2CH2CH2•
Termination reactions, which happen when two free radicals react with each other to produce products that are not free radicals. Two common forms of termination are recombination, where the two radicals combine to form one larger molecule, and disproportionation, where one radical transfers a hydrogen atom to the other, giving an alkene and an alkane.
CH3• + CH3CH2• → CH3CH2CH3
CH3CH2• + CH3CH2• → CH2=CH2 + CH3CH3
Thermal cracking is an example of a reaction whose energetics are dominated by entropy (∆S°) rather than by enthalpy (∆H°) in the Gibbs Free Energy equation ∆G°=∆H°-T∆S°. Although the bond dissociation energy D for a carbon-carbon single bond is relatively high (about 375 kJ/mol) and cracking is highly endothermic, the large positive entropy change resulting from the fragmentation of one large molecule into several smaller pieces, together with the extremely high temperature, makes T∆S° term larger than the ∆H° term, thereby favoring the cracking reaction.
Here is an example of cracking with butane CH3-CH2-CH2-CH3
1st possibility (48%): breaking is done on the CH3-CH2 bond.
CH3* / *CH2-CH2-CH3
after a certain number of steps, we will obtain an alkane and an alkene: CH4 + CH2=CH-CH3
2nd possibility (38%): breaking is done on the CH2-CH2 bond.
CH3-CH2* / *CH2-CH3
after a certain number of steps, we will obtain an alkane and an alkene from different types: CH3-CH3 + CH2=CH2
3rd possibility (14%): breaking of a C-H bond
after a certain number of steps, we will obtain an alkene and hydrogen gas: CH2=CH-CH2-CH3 + H2 this is very useful since the catalyst can be recycled.
Wednesday, March 25, 2009
Process of rose water
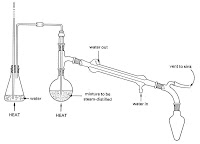
Distillation
In the process of distillation, large stills, traditionally of copper, are filled with roses and water. The still is fired for 60-105 minutes. The vaporized water and rose oil exit the still and enter a condensing apparatus and are then collected in a flask. This distillation yields a very concentrated oil, direct oil, which makes up about 20% of the final product. The water which condenses along with the oil is drained off and redistilled, cohobation, in order to obtain the water-soluble fractions of the rose oil such as phenyl ethyl alcohol which are a vital component of the aroma and which make up the large bulk, 80%, of the oil. The two oils are combined and make the final rose otto.
Rose otto is usually dark olive-green in color and will form white crystals at normal room temperature which disappear when the oil is gently warmed. It will tend to become more viscous at lower temperatures due to this crystallization of some of its components.
The essence has a very strong odor, but is pleasant when diluted and used for perfume. Attar of roses was once made in India, Persia, Syria, and the Ottoman Empire. The Rose Valley in Bulgaria, near the town of Kazanlak, is among the major producers of attar of roses in the world.[2]
Due to the heat required for distillation, some of the compounds extracted from the rose undergo denaturing or chemical breakdown. As such, rose otto does not smell very similar to "fresh" roses.
The hydrosol portion of the distillate is known as rosewater. This inexpensive by-product is used widely as a food flavoring as well as in skin care.
Solvent extraction
In the solvent extraction method, the flowers are agitated in a vat with a solvent such as hexane , which draws out the aromatic compounds as well as other soluble substances such as wax and pigments. The extract is subjected to vacuum processing which removes the solvent for re-use. The remaining waxy mass is known as a concrete. The concrete is then mixed with alcohol which dissolves the aromatic constituents, leaving behind the wax and other substances. The alcohol is low-pressure evaporated, leaving behind the finished absolute. The absolute may be further processed to remove any impurities that are still present from the solvent extraction.
Rose absolute is a deep reddish brown with no crystals. Due to the low temperatures in this process, the absolute may be more faithful to the scent of the fresh rose than the otto.
CO2 extraction
A third process, supercritical carbon dioxide extraction, combines the best aspects of the other two methods. When carbon dioxide is put under high pressure, it becomes a liquid. (Under normal pressure CO2 changes directly from a solid to a gas in a process known as sublimation.) The liquid CO2 extracts the aromatics from the plant material.
Like solvent extraction, the CO2 extraction takes place at a low temperature, extracts a wide range of compounds rendering an essence more faithful to the original, and leaves the aromatics unaltered by heat. Because CO2 is gas at normal atmospheric
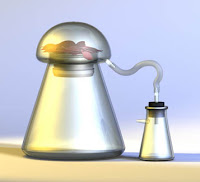
Purification of Water
Boiling: Water is heated hot enough and long enough to inactivate or kill micro-organisms that normally live in water at room temperature. Near sea level, a vigorous rolling boil for at least one minute is sufficient. At high altitudes (greater than two kilometers or 5000 feet) three minutes is recommended.[17] In areas where the water is "hard" (that is, containing significant dissolved calcium salts), boiling decomposes the bicarbonate ions, resulting in partial precipitation as calcium carbonate. This is the "fur" that builds up on kettle elements, etc., in hard water areas. With the exception of calcium, boiling does not remove solutes of higher boiling point than water and in fact increases their concentration (due to some water being lost as vapour). Boiling does not leave a residual disinfectant in the water. Therefore, water that has been boiled and then stored for any length of time may have acquired new pathogens.
Granular Activated Carbon filtering: a form of activated carbon with a high surface area, absorbs many compounds including many toxic compounds. Water passing through activated carbon is commonly used in municipal regions with organic contamination, taste or odors. Many household water filters and fish tanks use activated carbon filters to further purify the water. Household filters for drinking water sometimes contain silver to release silver ions which have an anti-bacterial effect.
Distillation involves boiling the water to produce water vapour. The vapour contacts a cool surface where it condenses as a liquid. Because the solutes are not normally vaporised, they remain in the boiling solution. Even distillation does not completely purify water, because of contaminants with similar boiling points and droplets of unvaporised liquid carried with the steam. However, 99.9% pure water can be obtained by distillation.
Reverse osmosis: Mechanical pressure is applied to an impure solution to force pure water through a semi-permeable membrane. Reverse osmosis is theoretically the most thorough method of large scale water purification available, although perfect semi-permeable membranes are difficult to create. Unless membranes are well-maintained, algae and other life forms can colonize the membranes.
The use of iron in removing arsenic from water. See Arsenic contamination of groundwater.
Direct contact membrane distillation (DCMD). Applicable to desalination. Heated seawater is passed along the surface of a hydrophobic polymer membrane. Evaporated water passes from the hot side through pores in the membrane into a stream of cold pure water on the other side. The difference in vapour pressure between the hot and cold side helps to push water molecules through.
Gas hydrate crystals centrifuge method. If carbon dioxide gas is mixed with contaminated water at high pressure and low temperature, gas hydrate crystals will contain only clean water. This is because the water molecules bind to the gas molecules at molecule level. The contaminated water is in liquid form. A centrifuge may be used to separate the crystals and the concentrated contaminated water.