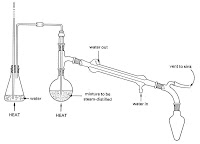
Distillation
In the process of distillation, large stills, traditionally of copper, are filled with roses and water. The still is fired for 60-105 minutes. The vaporized water and rose oil exit the still and enter a condensing apparatus and are then collected in a flask. This distillation yields a very concentrated oil, direct oil, which makes up about 20% of the final product. The water which condenses along with the oil is drained off and redistilled, cohobation, in order to obtain the water-soluble fractions of the rose oil such as phenyl ethyl alcohol which are a vital component of the aroma and which make up the large bulk, 80%, of the oil. The two oils are combined and make the final rose otto.
Rose otto is usually dark olive-green in color and will form white crystals at normal room temperature which disappear when the oil is gently warmed. It will tend to become more viscous at lower temperatures due to this crystallization of some of its components.
The essence has a very strong odor, but is pleasant when diluted and used for perfume. Attar of roses was once made in India, Persia, Syria, and the Ottoman Empire. The Rose Valley in Bulgaria, near the town of Kazanlak, is among the major producers of attar of roses in the world.[2]
Due to the heat required for distillation, some of the compounds extracted from the rose undergo denaturing or chemical breakdown. As such, rose otto does not smell very similar to "fresh" roses.
The hydrosol portion of the distillate is known as rosewater. This inexpensive by-product is used widely as a food flavoring as well as in skin care.
Solvent extraction
In the solvent extraction method, the flowers are agitated in a vat with a solvent such as hexane , which draws out the aromatic compounds as well as other soluble substances such as wax and pigments. The extract is subjected to vacuum processing which removes the solvent for re-use. The remaining waxy mass is known as a concrete. The concrete is then mixed with alcohol which dissolves the aromatic constituents, leaving behind the wax and other substances. The alcohol is low-pressure evaporated, leaving behind the finished absolute. The absolute may be further processed to remove any impurities that are still present from the solvent extraction.
Rose absolute is a deep reddish brown with no crystals. Due to the low temperatures in this process, the absolute may be more faithful to the scent of the fresh rose than the otto.
CO2 extraction
A third process, supercritical carbon dioxide extraction, combines the best aspects of the other two methods. When carbon dioxide is put under high pressure, it becomes a liquid. (Under normal pressure CO2 changes directly from a solid to a gas in a process known as sublimation.) The liquid CO2 extracts the aromatics from the plant material.
Like solvent extraction, the CO2 extraction takes place at a low temperature, extracts a wide range of compounds rendering an essence more faithful to the original, and leaves the aromatics unaltered by heat. Because CO2 is gas at normal atmospheric
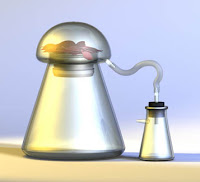
Purification of Water
Boiling: Water is heated hot enough and long enough to inactivate or kill micro-organisms that normally live in water at room temperature. Near sea level, a vigorous rolling boil for at least one minute is sufficient. At high altitudes (greater than two kilometers or 5000 feet) three minutes is recommended.[17] In areas where the water is "hard" (that is, containing significant dissolved calcium salts), boiling decomposes the bicarbonate ions, resulting in partial precipitation as calcium carbonate. This is the "fur" that builds up on kettle elements, etc., in hard water areas. With the exception of calcium, boiling does not remove solutes of higher boiling point than water and in fact increases their concentration (due to some water being lost as vapour). Boiling does not leave a residual disinfectant in the water. Therefore, water that has been boiled and then stored for any length of time may have acquired new pathogens.
Granular Activated Carbon filtering: a form of activated carbon with a high surface area, absorbs many compounds including many toxic compounds. Water passing through activated carbon is commonly used in municipal regions with organic contamination, taste or odors. Many household water filters and fish tanks use activated carbon filters to further purify the water. Household filters for drinking water sometimes contain silver to release silver ions which have an anti-bacterial effect.
Distillation involves boiling the water to produce water vapour. The vapour contacts a cool surface where it condenses as a liquid. Because the solutes are not normally vaporised, they remain in the boiling solution. Even distillation does not completely purify water, because of contaminants with similar boiling points and droplets of unvaporised liquid carried with the steam. However, 99.9% pure water can be obtained by distillation.
Reverse osmosis: Mechanical pressure is applied to an impure solution to force pure water through a semi-permeable membrane. Reverse osmosis is theoretically the most thorough method of large scale water purification available, although perfect semi-permeable membranes are difficult to create. Unless membranes are well-maintained, algae and other life forms can colonize the membranes.
The use of iron in removing arsenic from water. See Arsenic contamination of groundwater.
Direct contact membrane distillation (DCMD). Applicable to desalination. Heated seawater is passed along the surface of a hydrophobic polymer membrane. Evaporated water passes from the hot side through pores in the membrane into a stream of cold pure water on the other side. The difference in vapour pressure between the hot and cold side helps to push water molecules through.
Gas hydrate crystals centrifuge method. If carbon dioxide gas is mixed with contaminated water at high pressure and low temperature, gas hydrate crystals will contain only clean water. This is because the water molecules bind to the gas molecules at molecule level. The contaminated water is in liquid form. A centrifuge may be used to separate the crystals and the concentrated contaminated water.